1979 F250 Rebuild / Cummins conversion
#34
Inching along painfully slow, but at least it isn't stalled...
Work has been keeping me extremely busy most of the time. But I need to take the work while it is available... many aren't so lucky in these times.
I did get the driver's side floorpan repaired and the entire cab rustproofed. The bare cab is on the frame. Woohoo! I also got both doors repaired. Each door had small rust pinholes in the lower corners of both sides. I repaired them all by leadwork, the most permanent fix I have ever used. Now the doors are back on the cab but need to be re-aligned and to have the insides rustproofed... when I get some time
One spot just before doing leadwork:

Another area after leadwork is done:
Work has been keeping me extremely busy most of the time. But I need to take the work while it is available... many aren't so lucky in these times.
I did get the driver's side floorpan repaired and the entire cab rustproofed. The bare cab is on the frame. Woohoo! I also got both doors repaired. Each door had small rust pinholes in the lower corners of both sides. I repaired them all by leadwork, the most permanent fix I have ever used. Now the doors are back on the cab but need to be re-aligned and to have the insides rustproofed... when I get some time

One spot just before doing leadwork:
Another area after leadwork is done:
#35

I am still unsure of whether I will be using the in-cab tank, the mid-mount tank, the rear mount tank, or some combination of them. I have all three styles of tanks in my stash of parts.
#36
#37
Last weekend I finally got to spend a few hours of quality time with the project... got the doors aligned to the cab. Also temporarily mounted the inner fenders and core support... The stock ford radiator clears the cummins fan nicely. Fortunately I measured everything correctly when determining the engine location! Now it is time to look into the CAC mods.
#38
Put in a radiator this evening and measured a good 1-5/8" between the fan blades and radiator core.
There is about 1" between the fan blades and radiator tanks.
The 2nd gen Dodge (1994~2001 or so) intercooler is too wide to fit without relocating the battery trays (which I do not want to do).
A 1998 powerstroke intercooler fits nicely as does a first gen Dodge (1991.5~1993). Powerstroke intercooler is a bit taller and looks more effective, so I am leaning in that direction.
Now I need to pick up a 4" dia holesaw bit for the core support...
There is about 1" between the fan blades and radiator tanks.

The 2nd gen Dodge (1994~2001 or so) intercooler is too wide to fit without relocating the battery trays (which I do not want to do).
A 1998 powerstroke intercooler fits nicely as does a first gen Dodge (1991.5~1993). Powerstroke intercooler is a bit taller and looks more effective, so I am leaning in that direction.
Now I need to pick up a 4" dia holesaw bit for the core support...
#39
I used a 1st gen in my truck and I think it wouldn't take too much to make the powerstroke ic fit. If you are using the 79 grill it should be easier than the 77 I have in mine. There is more open space in the center of the 78/9 grills.
When I shaved down my grill inserts I just used the cordless dewalt grinder with a thin cutting wheel. It worked very well, the tiny little bit of plastic the melted during the cutting peels right off and leaves a nice clean cut. I liked the cordless because it has a variable speed trigger. I think you could get the same results from a die grinder but I've never used one.
When I shaved down my grill inserts I just used the cordless dewalt grinder with a thin cutting wheel. It worked very well, the tiny little bit of plastic the melted during the cutting peels right off and leaves a nice clean cut. I liked the cordless because it has a variable speed trigger. I think you could get the same results from a die grinder but I've never used one.
#40
Stopped at a local welding supply to pick up tungstens as well as some filler rod so now 
I CAN TIG WELD!

I had to relocate the upper mounts of the powerstroke intercooler so it fits up against the core support better. Slight clearancing of the core support was necessary (ball peen hammer) at the upper corners of the header tanks.

The TIG welds aren't perfect, but they certainly are strong enough to keep the intercooler in place. Not too bad for my first TIG weld job ever...

I was able to make a simple bolt-on steel bracket that utilizes the intercooler's existing lower mount bosses:

Next is the other side's lower mount bracket. I just need more time for this project

I CAN TIG WELD!

I had to relocate the upper mounts of the powerstroke intercooler so it fits up against the core support better. Slight clearancing of the core support was necessary (ball peen hammer) at the upper corners of the header tanks.
The TIG welds aren't perfect, but they certainly are strong enough to keep the intercooler in place. Not too bad for my first TIG weld job ever...
I was able to make a simple bolt-on steel bracket that utilizes the intercooler's existing lower mount bosses:
Next is the other side's lower mount bracket. I just need more time for this project

#41
I have read many many posts on several forums about the problem. I even read a quote taken from a Detroit Diesel manual. But I have yet to read anything from anyone who actually had any of the problems everyone talks about. I have read about several conversions that used good, clean, stock galvanized tanks without any problems at all. So I ain't skeered...
I am still unsure of whether I will be using the in-cab tank, the mid-mount tank, the rear mount tank, or some combination of them. I have all three styles of tanks in my stash of parts.

I am still unsure of whether I will be using the in-cab tank, the mid-mount tank, the rear mount tank, or some combination of them. I have all three styles of tanks in my stash of parts.
#42
progress report
Made more progress the last few days as we got rained out at work. I fabbed up the other intercooler mount. I modified the turbocharger outlet elbow to shorten it as well as make it point more towards the intercooler.

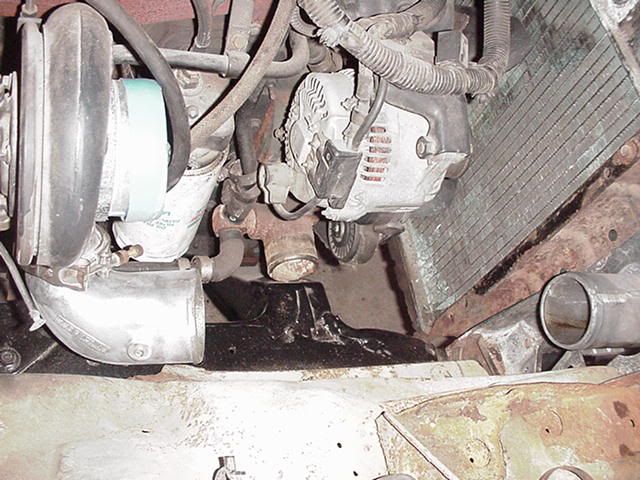
I TIG welded the two intercooler pipes out of some used Ford medium duty truck aluminum tubes I had. I can use standard intercooler boots for a medium duty Ford application. Also made up the lower radiator steel pipe that snakes around to connect the Dodge application lower water connection on the 6BT to the Ford radiator. Here is my initial mockup - using an air preheater hose since it is easily bendable, holds its shape, and is even the right diameter

I will need to reverse the connections of the radiator tanks to the opposite sides yet. No big deal, I have done that before on other projects...
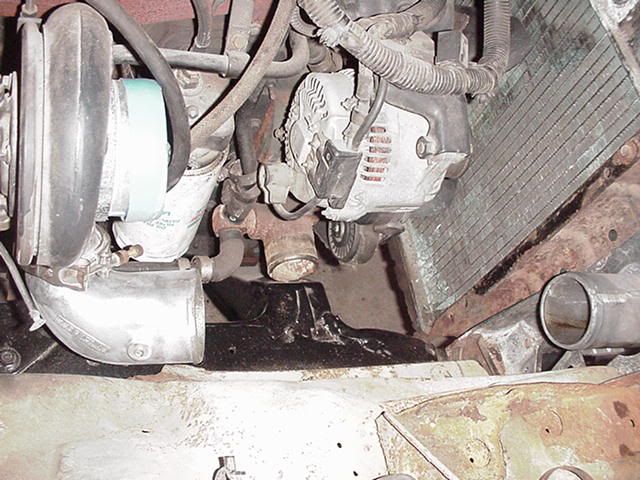
I TIG welded the two intercooler pipes out of some used Ford medium duty truck aluminum tubes I had. I can use standard intercooler boots for a medium duty Ford application. Also made up the lower radiator steel pipe that snakes around to connect the Dodge application lower water connection on the 6BT to the Ford radiator. Here is my initial mockup - using an air preheater hose since it is easily bendable, holds its shape, and is even the right diameter

I will need to reverse the connections of the radiator tanks to the opposite sides yet. No big deal, I have done that before on other projects...
#43
picture updates
Fabricated a snaking pipe to connect the Ford radiator to the Dodge application Cummins lower water connection. Pipe was originally from a Cummins-powered Ford medium duty truck. Cut out the bend sections and re-welded it together as I needed it. Recycling at its finest
The stepped hose is the end of the original radiator hose from the 1994 Dodge donor truck. Other end points towards the lower radiator tank where I will relocate the connection at.

Here's one of the CAC tubes, the one for the cool side:

I also fabbed up a quick mounting plate for the air filter box. I wanted to use the stock air filter because I already have it, it fits nicely under the hood, and I like the filter minder. More recycling... I made the bracket a little longer at one end with a pair of through holes for attaching a turbocharger heat shield - probably not necessary but easy enough to add.

Here's one of the CAC tubes, the one for the cool side:
I also fabbed up a quick mounting plate for the air filter box. I wanted to use the stock air filter because I already have it, it fits nicely under the hood, and I like the filter minder. More recycling... I made the bracket a little longer at one end with a pair of through holes for attaching a turbocharger heat shield - probably not necessary but easy enough to add.
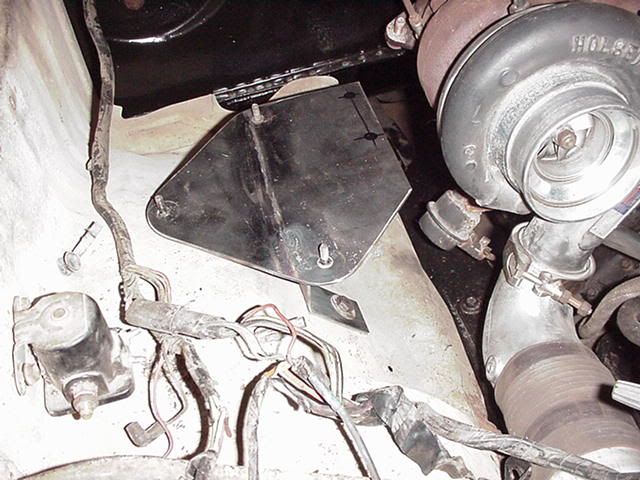
#44
Glad to see you are back at it! Great job recycling parts from other apps. The ford intercooler looks great, does the hood latch still fit? I like your snaked radiator tube I did just about the same thing except took it to the stock location. I used bends from a pole pig cooling tubes. Yours came out looking oem great job.Good idea on shortening and turning the turbo outlet. You have the KISS principal dialed!!!!!!!!!! Reusing the stock air filer sounds good to me
